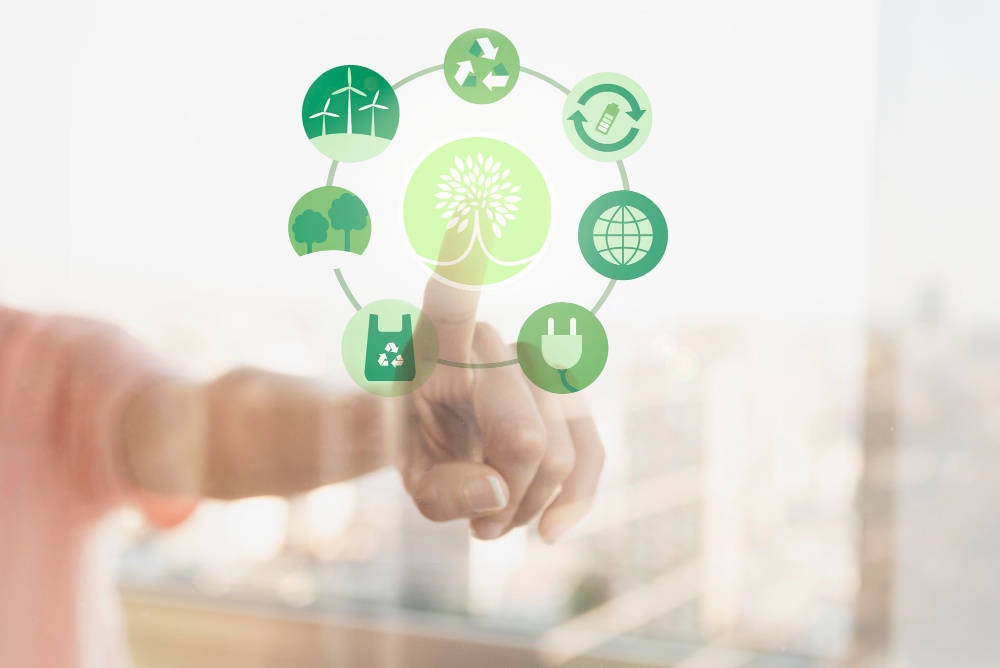
Quels sont les effets de l’isolation thermique sur l’environnement ?
L’isolation thermique est-elle écologique ? Comment évaluer l’impact environnemental d’une action d’isolation sur un bâtiment industriel ? On revient sur le principe de ces opérations et sur leurs applications possibles dans l’industrie.
Pourquoi l’isolation thermique est-elle écologique ?
L’isolation thermique est écologique dans la mesure où elle permet de réduire les consommations en énergie nécessaires au maintien d’une température de fonctionnement et de confort.
Pour offrir des conditions de travail optimales aux salariés, les locaux sont chauffés en hiver. Si le bâtiment est mal isolé ou souffre de plusieurs défauts d’étanchéités localisés, la facture de chauffage de l’entreprise risque d’être très salée pour un confort thermique pourtant médiocre. Dans ce cas de figure, des travaux d’isolation peuvent inverser la situation. Il sera alors possible de chauffer plus efficacement en dépensant moins d’énergie.
Le même principe vaut pour les installations de chauffage et de refroidissement des sites industriels. Ici, l’isolant est posé tout au long des canalisations afin de réduire les échanges thermiques avec les espaces intérieurs ou extérieurs. On parle alors de calorifugeage. Après travaux, le site consomme moins d’énergie pour atteindre et conserver de très hautes ou de très basses températures (étuves, fours industriels, coffres cryogéniques…).
Ces opérations d’isolation ont un impact sur l’environnement positif, puisqu’elles réduisent la consommation d’énergie, elle-même à l’origine d’émissions en gaz à effet de serre (GES).
La haute performance énergétique dans l’industrie
Tous les secteurs (résidentiel, tertiaire, industriel) sont engagés dans une dynamique de réduction des dépenses énergétiques.
Ces démarches sont bénéfiques pour les usagers et pour les entreprises qui profitent d’installations plus efficaces et moins coûteuses, mais aussi pour l’environnement grâce à la meilleure maîtrise des consommations en énergie.
Pour les industriels, le potentiel d’optimisation des dépenses et d’amélioration du bilan carbone des activités est particulièrement important. La haute performance leur permet de mieux maîtriser leur budget et de s’inscrire dans l’industrie de demain.
Le choix des matériaux d’isolation des bâtiments industriels
Tous les matériaux d’isolation des bâtiments et de leurs installations n’ont pas le même impact sur l’environnement. La nature biosourcée ou pétrochimique du matériau peut par exemple influencer la recyclabilité en fin de cycle de vie.
Plusieurs axes sont possibles pour améliorer les performances énergétiques des industriels. S’agissant de l’isolation d’un local d’activité accueillant les salariés, tous les types de matériaux isolants sont envisageables à condition de respecter l’équilibre global de la construction.
Pour l’isolation des installations ou des ouvrages soumis à de très fortes variations thermiques, le spectre des solutions se resserre. Sur une canalisation qui transporte des fluides à très haute température, la priorité est de trouver des complexes isolants compatibles. Quelle que soit la composition de l’isolant, le seul gain de performance énergétique permis par le calorifugeage contribue à réduire l’impact sur l’environnement.